International Facility of the Year: Mr. Storage,Santiago, Chile
When you think of Santiago, Chile, you might think of the beautiful mountains that surround the city, the Plaza de Armas (city center), shopping in the boutiques or the vibrant nightlife.
However, Grupo PATIO, owner and developer of Mr. Storage, wants you to think of super-high end storage facilities that will change the landscape of self-storage in Santiago.
The company’s first development, Mr. Storage, which is located in an affluent residential suburb of the city was five years in planning, development and construction and offers many of the high end amenities the company hopes to become known for including the country’s first (known) wine storage facility, beautiful construction and state of the art security.
Santiago actually has at least 40 other self storage facilities with about 1.5 million square feet of storage space constructed, says Jaime Diaz Garcia, regional director for Groupo PATIO. “The self storage industry is actually growing very rapidly,” said Garcia. “The industry is concentrated in three major operators. It’s really been developing at a rapid pace. Some are state of the art, some are just containers with not many services. The industry has been evolving since around 2000.”
The Groupo PATIO Philosophy
Grupo PATIO formed in 2011 with an eye on changing the face of self storage in Santiago. Garcia, who has a decade of experience in the self storage industry, was hired to help the company identify and develop the company’s self storage facilities.
Garcia said the company identified three main goals before seeking a site for its first development:
1). Build state of the art facilities
2). Develop self storage facilities that are near the customers. Previously, many self storage facilities in Santiago were built in industrial areas that customers had to drive some distances to reach.
3). Build quality self storage facilities, not necessarily the biggest. Standards are most important to the company.
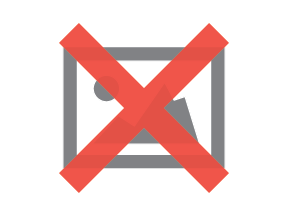
In its quest to build one of the best state of the art facilities in Santiago as its first project, representatives from Grupo PATIO not only toured the best facilities in Chili, but also attended the ISS show multiple times and assisted with the ISS world expo and took many tours of state of the art facilities in the United States. “We studied the best practices of some of the most successful facilities in the U.S. before beginning our own,” said Garcia.
The company identified the property they wanted to purchase in 2012. Garcia said the land had previously been evaluated for self storage, but the competing company failed to follow through on its evaluation of the property.
Garcia explained that the seller owns the surrounding Piedra Rojas Developments, which came with restrictions that the land couldn’t be used for other retail or commercial developments.
“This is a very high end community, so we thought this would be a good place to start,” said Garcia. “There was a lack of self storage in the area.”
Grupo PATIO thought they would be up and running by 2013, but the best laid plans sometimes have a long delay and the realization of Mr. Storage wouldn’t come to fruition until 2017.
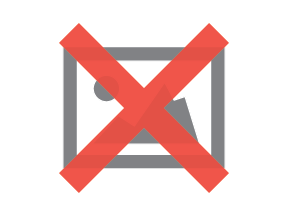
The Devil is in the Details
What the previous owner failed to disclose was a myriad of challenges that awaited anyone wanting to develop the land. What was thought to be a perfect property that would get regulatory approval quickly ended up being a four year long journey for the company that required them to seek regulatory approval from almost every governmental agency in Santiago.
The first major obstacle was presented when the company learned there is a canal on the back side of the land. “We realized that we could never build a facility on that land because the restrictions actually occupied two-thirds of that land,” said Garcia. The process of resolving that restriction was finally resolved in 2016, but not after much paperwork and a regulation that stated the company couldn’t build on more than 56 percent of the land, which meant the company lost more than half of the construction potential.
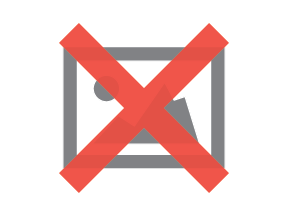
Grupo PATIO thought they had that problem solved when the company’s architects suggested building a multi-story building. “When we applied for a five floor building approval, the city rejected it because of the existence of an aerodome (a small airport) near the facility so we had to reduce the building to a three story building and ask the national aeronautic civil office to approve it,” Garcia said.
The next challenge came in the soil samples. “Once we had a three level building approved, by law in Chile, because of the earthquakes, we needed to drill at least 30 meters deep and take samples of the land to analyze the quality of the soil,” said Garcia. “The results came up showing we had the worst kind of soil to build.”
This meant digging 13 feet deep and removing 21,500 square feet of soil, almost 282,500 cubic units of dirt and refilling it with approved quality dirt. “It was getting very complicated and at some point, we began to think we had just bought a bad piece of land,” said Garcia.
But Garcia said that at one of those points, the competitor who had previously not bought the land approached him and congratulated them on securing that location for the project. “We have a very good relationship with our competitors,” said Garcia. “They couldn’t buy it because it was too high and they didn’t think it would bring a good ROI.”
Garcia said they had confidence, even with all of the challenges, extra costs and delays that they had secured the right piece of property. “Grupo PATIO was very confident and if we had a little extra cost, that is the price we had to pay.”
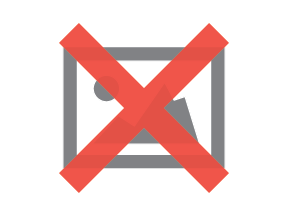
The State of the Art Design
Since the location is in an affluent residential suburb, Mr. Storage had to be designed so that it fit into the neighborhood. “Our first and foremost priority was to get our clients attention without disturbing the neighborhood and it suburban atmosphere,” said Garcia. “Not only did we have to avoid conflict by our neighbors, but we had to be welcomed by them. Local authorities in Chile are very receptive to community demands and this could have caused construction several obstacles and setbacks.”
Francisco Vares Palma, architect with VARASARQ in Santiago, designed the plans for Mr. Storage with a less industrial look. “We preferred a warmer image that would be fitting for our neighbors,” said Palma. “Our client also wanted to redefine what self storage in Chile had been doing for years and that was also considered in the design from the beginning.”
Palma designed a wooden look path work ventilated façade that created a friendlier and more welcoming appeal, while also increasing energy use efficiency.
The next priority for the building was to build to LEED standards, which requires a number of energy efficiency building practices including using energy efficient materials, water efficiency and other energy efficient standards. “We wanted to work to become LEED certified, but it was really cost prohibitive,” said Garcia.
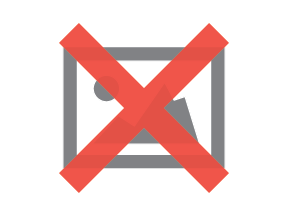
Instead, Mr. Storage is built to many of the LEED standards, including:
Hydric Efficiency
- Natural landscaping. Garcia said they chose low maintenance landscaping with native species such as species of cactuses, little bushes and trees that don’t need watered on a daily basis. “They resemble the natural landscaping found in the Chicureo area,” said Garcia. “Since we have experienced some climatic changes, we specifically selected these species that have characteristics of adapting to extreme climate, so there’s no need for a big maintenance budget.”
- Low flow toilets and faucets. The ones chosen for the site help reduce the water needed during operation by 30 percent. “To wash your hands, we have push button faucets to avoid leaks and waste water inefficiency,” Garcia said.
Energy Efficiency
- Façade construction. The patchwork ventilated façade is made of fiber cement. Underneath the façade, the entire building is covered with a high insulating metal sandwich panel, which keeps the inside a permanent, comfortable temperature. “Although the panel doesn’t have an energy efficiency rating, its insulation is made of a 40 millimeter expanded polyurethane, that makes its thermal conductivity as low as 0.025,” Garcia said. “Our energy efficiency is based on a mix of shielding materials and smart architectural design that optimizes the local weather conditions. We let a controlled amount of sunlight enter our hallways to increase temperature and have natural ventilation throughout the entire building. Renewing interior air, making climate control necessary.”
High Efficiency Illumination and Control Systems
- Interior lighting controls. All of the lighting in Mr. Storage are on timer control and usage/consumption control. There are motion sensors in every hallway that illuminate that hallway when needed. There are LED lights inside each unit that only turn on when the roll up door is fully opened. These sensors are available on Janus roll up doors. “This is a very practical solution for tenants and for operation control purposes,” said Garcia
- Exterior lighting controls. The exterior lights in the parking lot, as well as on the signage are on a program panel that turns on and shuts off the lights at specific times of the day.
Building Materials
- Building materials with recycled components. As part of the construction process, Group PATIO hired a consultant company, POCH, which was in charge of overseeing the construction process. As the company initially was going to try for LEED certification, they were also in charge of overseeing that process as well. “They contacted companies that supply energy efficient construction materials that contributed to the construction and operation standards we were looking for,” said Garcia. “This led to finding materials that also had recycled materials.”
- Recyclable material separation inside the property. Garcia said it isn’t typical in Chile to do recycling of construction material, so this was really a ground breaking piece of the sustainable practices used. “Most are sent to certified sites that receive debris and other left overs of construction,” said Garcia. Metal rod cuts, pipelines and wood planks for concrete molding were all donated to the families of construction workers for their own home improvements and home additions.
- Sustainable Construction process. Processes were put into place on the site so as not to affect the quality of life in the surrounding community, such as keeping construction noise to a minimum and making sure any materials were not littering the neighborhood.
Sustainable Operations
- Garcia said one of the issues in Chile is making sure construction sites are safe for workers. Groupo PATIO took this very seriously. “The construction chamber in Chile has been very focused on eliminating human risks during construction, thy want to protect more of the personnel that works during construction because there has been a lot of injuries and deaths,” Garcia said. The construction company, PITAGORA, hired a Risk Manager to oversee safety. Group PATIO also hired another Risk Manager to have more eyes on the site. The company not only complied with all of the safety laws, but took it a step further. Other rules, such as no smoking on the site were also implemented. “Construction personnel in Chile is very poorly trained and educated and they don’t see the risk of smoking or working with safety measures or equipment, so it is an issue here to get people to understand the risks of construction.”
Sergio Wilson Porter, operations manager for PITAGORA said the main challenge his company faced was the deadline and the fact it was built in a residential neighborhood. “Thanks to the performance of the professionals who worked on the project, the construction was successfully fulfilled,” said Porter. “The project was designed and built with a respect for the environment and with the concern of affecting it as little as possible during construction.”
Janus International provided the interior systems for the project. “We had to hire a certified team of installers and fly them from Mexico to Chile to do the installation work,” said Garcia. “There is no certified installation company that could do the work as specified by Janus”
Not only did this add cost to the project, but Garcia said the logistics of brining in an entire crew from Mexico is complex due to labor regulations and working visas. “It was a challenge to get everything timed right so we had them here and ready to work to avoid delays and extra costs of hotels,” said Garcia.
While this did add an extra cost to the project, Garcia said it was well worth the expense. “We knew that Usted Guarda, the company hired from Mexico to fly the crew to Chile had an exceptional track record of installing Janus hallway solutions and rollup doors, so we knew the cost would be absolutely covered when we opened the facility.”
The security system by PTI Security Systems is state of the art with two keypads to enter the building and two for the storage area. Groupo PATIO also had to hire other contractors from Usted Guarda in Mexico for the installation, as Garcia said the system is not common in Chile.
“One of the things we’re really proud of at PTI is out international presence. We have world class installation partners around the world, and we have a great partner in South America,” said Christine DeBord, marketing and resale channel manager. “Mr. Storage is using a robust and fully integrated PTI security system to protect their investment, attract new tenants, and ensure that their facility is safe and secure day and night.”
Marketing into the Future
Groupo PATIO hired two employees for the Mr. Storage facility and part of their job is to reach out to the surrounding community making the Mr. Storage brand name known. They also hired two marketing companies, one specifically to work on the website and another to market the brand on social media.
Mr. Storage is currently at 7% occupancy and hopes to reach 20% by the end of the year and 50% a year from now. Garcia said they hope to do this by using a substantial portion of the marketing budget on social media, as well as SEO/SEM optimization, move in specials and partnerships with moving local moving companies.
Development Team
Builder – Constructora Pitagora, Santiago, Chile
Architect – VaeasArq, Vitacura, Santiago, Chile
Management Software – SiteLink, Raleigh, NC
Security – PTI Security Systems, Scottsdale, AZ
Doors & Interior System – Janus International, Temple, GA
Door Hardware – Chateau Products, Bradenton, FL
Development Team
Builder – Constructora Pitagora, Santiago, Chile
Architect – VaeasArq, Vitacura, Santiago, Chile
Management Software – SiteLink, Raleigh, NC
Security – PTI Security Systems, Scottsdale, AZ
Doors & Interior System – Janus International, Temple, GA
Door Hardware – Chateau Products, Bradenton, FL
Kerri Fivecoat-Campbell is a freelance journalist based in the Ozark Mountains. She is a regular contributor to MiniCo’s publications. Her business articles have also appeared in Entrepreneur, Aol.com, MSN.com, and The Kansas City Star.
More Content
Popular Posts
Recent Posts
Senate Bill 709 (SB709) has many in the...
In January, self-storage industry veteran...
In April 1984, the first non-stop commercial...
Raise your hand if you’ve ever made plans,...
Everyone knows it: Investing in real estate...
They say when one door closes, another one...
Like its name implies, Surprise, Ariz., a...
Self-storage has become as reliant on the...
